Everything You Need to Know About Lift Maintenance
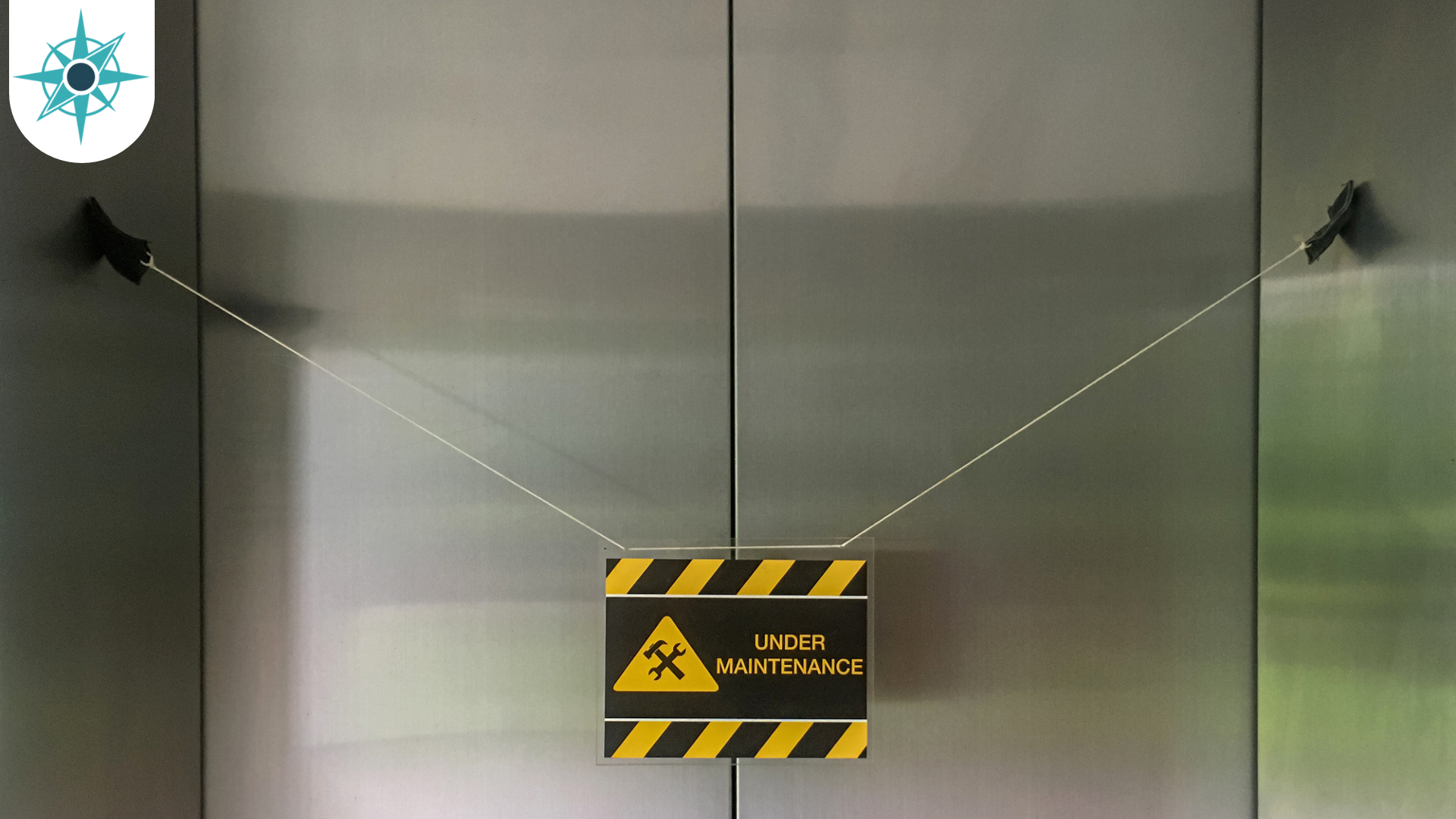
Lifts play a vital role in modern buildings, whether in offices, apartment buildings, hospitals or shopping centres, ensuring safe and efficient vertical transport for millions of people every day. A well-maintained lift not only ensures the safety and comfort of lift users; it also extends the system’s lifespan, reduces downtime, and ensures compliance with legal and insurance requirements. Whether you’re a building manager, property owner or facilities professional, understanding lift maintenance is crucial.
In this article, we will delve into lift maintenance in detail, explaining why it is important, the key steps involved in routine maintenance and how lift maintenance companies can help you keep up with compliance requirements.
Why Is Lift Maintenance Important?
Any facility or premises with a lift in operation must have a structured elevator maintenance plan in place to ensure the lift continues to operate reliably, safely and efficiently after installation.
Preventing Breakdowns
Lifts have been engineered with safety mechanisms to prevent falling in the event of a malfunction or breakdown. If a component fails, the lift will simply cease moving or halt its movement. Contrary to common misconception, there is no danger of the lift car plummeting down the shaft.
Even so, breakdowns are highly inconvenient. Whether used for convenience or out of necessity, passengers rely on lifts to reach their destinations, and any failure to do so can cause significant frustration and distress, particularly if they must wait for repairs to be carried out.
Lift maintenance plays a crucial role in mitigating such issues. Through regular inspections and preventative care, potential problems are identified and addressed before they can escalate into major operational failures. This helps minimise the likelihood of lift breakdowns, preventing the interrupted service of your lift.
Extending the Lifespan of Your Lift
Lifts that receive minimal servicing may begin to show signs of decline within just ten years of installation. Neglecting maintenance accelerates the degradation of critical components, increasing the likelihood of breakdowns, safety risks, and costly emergency repairs or full replacements much earlier than anticipated. In fact, studies show that lifts with scheduled servicing experience 30-50% fewer breakdowns per year compared to those maintained only when issues arise.
According to the Lift and Escalator Industry Association (LEIA), regular preventative maintenance is the most important factor in ensuring a lift reaches its full operational lifespan. With consistent maintenance, a lift can last between 20 and 25 years, and this can be extended to over 30 years with lift modernisation upgrades.
Routine maintenance is essential for preventing wear and tear from worsening, ensuring vital components are operating in optimal condition and identifying and addressing small issues before they turn into major failures.
Legal Compliance
Since lift systems are designed to transport people, they are subject to strict health and safety laws to keep lift passengers safe. These legal requirements often fall on the duty holder, who may be a landlord, building owner, facility manager or employer. It is their responsibility to ensure that all lifts are safe for both users and maintenance personnel.
Failing to meet legally required maintenance standards can lead to serious consequences, including prosecution and fines under health and safety laws.
What Are The Responsibilities of Duty Holders?
To meet legal compliance requirements and ensure any lifts remain in safe working condition, duty holders are obligated to undertake the following responsibilities:
Schedule Routine Examinations
Lifting Operations and Lifting Equipment Regulations1998 (LOLER) requires passenger lifts to be inspected every 6 months, while goods-only lifts every 12 months. These inspections must be conducted by a qualified and competent person, not the duty holder themselves. However, it is the responsibility of the duty holder to arrange these examinations, ensuring they are performed promptly and by a suitably qualified individual.
Keep Written Records
Duty holders must keep written records of all lift examinations and maintenance work for a minimum of two years. These records should be stored securely, ensuring they can be accessed and presented to the Health and Safety Executive (HSE) if requested, demonstrating compliance with legal maintenance obligations.
Respond to Risks
Any serious issues or defects identified during the bi-annual lift examinations must be reported to the HSE immediately. Appropriate action must then be taken to ensure the lift poses no risk to passengers, which often includes taking the lift out of service until the necessary repairs have been completed.
Ensure Safe Working Conditions
Under the Health and Safety at Work Act 1974 and the Provision and Use of Work Equipment Regulations 1998 (PUWER), the duty holder is responsible for ensuring that all lifts remain in safe working order. This includes ensuring that maintenance is carried out regularly, in accordance with the guidelines set out by the manufacturer.
How Does Lift Servicing Fit into Lift Maintenance?
Lift servicing is a planned, preventative elevator maintenance process that ensures a lift remains in safe and reliable working condition. Lift servicing, carried out by a qualified lift engineer, plays a key role in helping duty holders meet their compliance requirements.
What Does It Include?
Lift servicing involves a comprehensive range of technical checks, safety tests, cleaning, lubrication, and functional inspections of critical components. This includes essential elements such as brakes, door mechanisms, emergency features, lighting, and control panels, ensuring all are in optimal working condition.
Below is a quick breakdown of the individual tasks a lift engineer will perform during servicing to ensure your lift runs smoothly and meets safety standards:
Thorough Visual Inspection:
● Lift components, such as cables, pulleys, rails and doors, will be checked for visible damage or wear.
● Safety devices, such as limit switches, emergency stop buttons and interlocks are checked, ensuring they are present and working properly.
● The control panel, buttons and indicators will be tested, ensuring they work as intended and show no signs of wear.
Mechanical Components:
● Bolts, fasteners and connections are checked for any loosening or corrosion.
● The drive system, including the motor, gearbox and brake system, is inspected for smooth operation and no mechanical faults.
● Moving parts, such as rails and bearings, are lubricated according to the manufacturer’s guidelines to reduce friction and wear.
Electrical System:
● Safety sensors, like door sensors and overload sensors, are tested to ensure they trigger the correct actions.
● Lighting and emergency lighting systems are tested to ensure they provide adequate and reliable lighting.
● The wiring and electrical connections are inspected for signs of wear, fraying or corrosion.
● The condition of wiring, cables and insulation is checked for signs of overheating.
Safety Features:
● The emergency stop button is tested to ensure it halts the lift immediately.
● Fire alarm integrations and emergency evacuation procedures are tested to ensure operation.
Control Systems:
● The control panel is checked for any error codes or malfunctions.
● All buttons are tested for proper response, ensuring indicator lights work correctly.
Doors and Entrances:
● Door operation is checked, ensuring they open and close smoothly and align with the floor properly.
● The door opening and closing mechanisms are tested, ensuring they open and close fully and without obstruction.
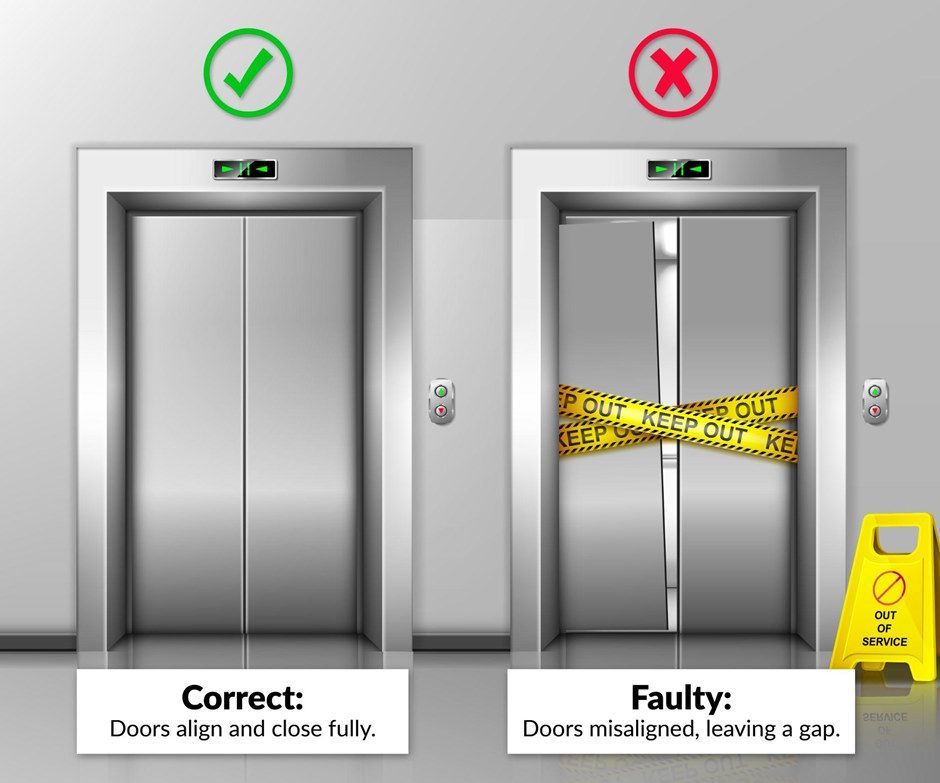
How Does Lift Servicing Help With Legal Compliance?
Lift servicing is not only vital for maintaining the safety and functionality of lifts, as well as extending their lifespan, but it also plays a key role in helping duty holders fulfil their legal obligations.
Lift servicing ensures legal compliance in several important ways:
● Ensuring lifts are in safe working condition: Through comprehensive inspections and testing of critical safety components, lift servicing ensures the lift maintains a safe operational condition as required under PUWER.
● Identifying and addressing defects: Regular inspections help identify potential defects or emerging faults. Upon completion of the inspection, the engineer will inform the duty holder about any issues, providing the necessary details to report them to the Health and Safety Executive (HSE). Additionally, the engineer will advise on the recommended course of action to resolve these issues, carrying out repairs on the spot where possible.
● Record keeping: During the lift service, the engineer documents their findings, actions taken, and any recommended repairs. These service records act as evidence that the lift is being properly maintained and can be crucial during audits or in the event of an HSE investigation.
Looking For Reliable Lift Maintenance Companies?
At ADL Lift Services, we’re proud to be one of the leading lift maintenance companies in Scotland, with over 80 years of combined experience in providing reliable lift servicing and repairs across the UK. Our team of qualified engineers specialises in elevator maintenance, ensuring that your lifts remain safe, operational, and fully compliant with all safety regulations.
We offer tailored maintenance plans, 24/7 emergency repair services, and expert advice to help prevent breakdowns and extend the lifespan of your lifts. With our commitment to quality and customer satisfaction, we are dedicated to keeping your lifts in optimal condition and ensuring peace of mind.
For more information about our elevator maintenance services, don’t hesitate to get in touch with us today!